Here’s what it’s like inside the Chicago-area factory aiming to end US overreliance on Asia’s PPE production
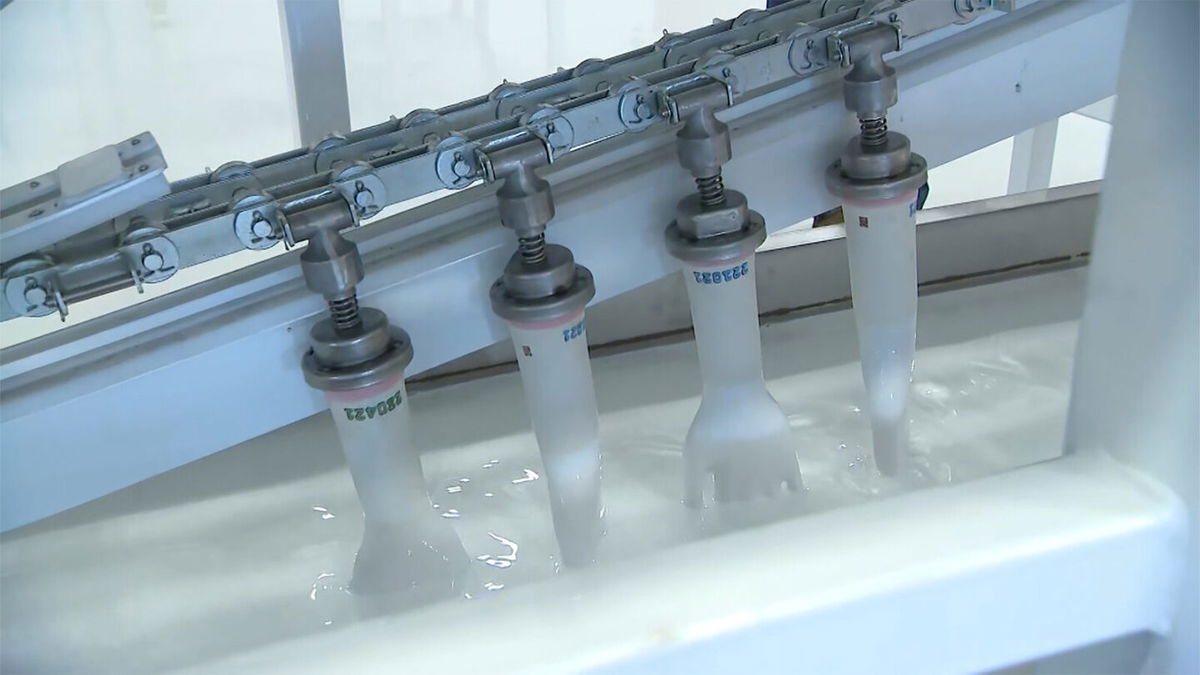
Nitrile gloves are "dipped" at the USMGC plant.
By Scott McLean and Jo Shelley, CNN
From the air, the former Caterpillar factory outside Chicago is sprawling — the size of two dozen football fields. Once a heavy equipment plant, it’s now a hive of activity making a product that has never been in higher demand: medical gloves.
The US Medical Glove Company, or USMGC, wants to turn a profit — but also to reduce US reliance on imports of medical gloves from the Far East, especially China and Thailand, while creating American jobs that pay well beyond the minimum wage.
It’s one of several US companies on the same mission: to make America more self-reliant on essential medical equipment after the coronavirus pandemic sparked a global scramble, especially for personal protective equipment, or PPE.
Inside USMGC’s facility, CEO Dylan Ratigan zips around the airplane hangar-sized “bays” in a golf cart, barely able to contain his excitement or his confidence in the company he’s building. The former cable news host has ambitions to produce 10 billion gloves per year, or nearing 3% of prepandemic global medical glove production capacity.
Ratigan felt compelled to act after seeing the United States desperately dependent on Asian PPE producers at the height of the pandemic, he told CNN. Amid the unprecedented demand, there were cases of price-gouging, fraud and scams. Dirty, used medical gloves even were imported to the US by the tens of millions, one CNN investigation found.
“I think bad decisions have been made in American manufacturing, specifically, for critical assets like (medical gloves),” Ratigan said. “The decision has been made to make sure that never happens again.”
Prepping — in America — for the next pandemic
During CNN’s visit in December to the USMGC factory, a newly built production line “dipped” its very first nitrile gloves — a test to make sure the machines work and the complex nitrile chemistry is just right. Every one of the line’s thousands of components are made in the United States, Ratigan said.
USMGC has a $63.6 million advance purchase order with the US government, the company announced in June. In all, the US government has contracts worth almost $700 million to invest in 11 American companies — enough, it hopes, to produce annually in the United States the equivalent of about 5% of prepandemic global glove production, a spokesperson for the Department of Health and Human Services, or HHS, told CNN in a statement.
The pandemic exposed “how dependent the US is on foreign sources which is a vulnerability in public health emergencies,” the HHS spokesperson said.
In 2020, 90% of gloves, syringes and needles used in the US were sourced from Asia alone, according to HHS. Now, Washington plans to spend $1.7 billion to spur domestic PPE production, part of $4.5 billion to help expand US manufacturing more broadly, according to HHS. The US is also investing in the domestic production of raw materials for gloves, masks, gowns, drugs, vaccines, medical test kits and other essential medical supplies.
Before the Covid-19 pandemic, there was only one company producing single-use nitrile gloves in the United States, that maker told CNN. SHOWA Group, a Japanese company, had about 125 employees at a factory in Fayette, Alabama, making about 400 million gloves annually. The production lines were old, and higher domestic costs made a box of gloves about twice the price of Asian brands, the company told CNN.
SHOWA Americas marketing director tried to convince buyers to diversify their suppliers by buying at least some American-made gloves, he said. It was a tough sell.
“We were trapped in the ever-frustrating game of being a domestic manufacturer — but our own country won’t buy our products,” Gilbert LeVerne explained.
Pre-pandemic plans to modernize and expand the factory have been accelerated thanks to the surge in demand and a loan from the US government. Within about three years, the company expects to produce more than six times its current US output, he said.
Meantime, a father-son start-up US Glove Supply is two months from firing up the machines at its new factory in Buffalo, New York, the company told CNN. It has no government orders or investment.
Neither does USA Gloves, a new company in suburban Houston started by former promotional product importers. CEO Zishan Momin and his partners started building their factory a year ago after finding it impossible to source gloves from abroad, he said.
Lacking any manufacturing experience, they enlisted help from foreign glove production experts, who will fire up the production lines next month. The gloves, they expect, will be a little bit more expensive than Asian brands.
“Hospitals and clinics and even end users are willing to pay that slight premium … so that we’re prepared for a future pandemic,” Momin told CNN.
Harnessing technology for a US-made glove
Malaysia produces the world’s largest share of medical gloves, followed by Thailand and China, according to the Malaysian Rubber Glove Manufacturers Association. It is near-impossible for US producers to compete with Asian factories on price. But imports often carry a different cost.
US Customs and Border Protection this year suspended imports from the world’s largest medical glove producer — Top Glove, in Malaysia — over accusations of forced labor. Only recently did imports resume after the company gave millions in back pay to its workers to rectify the agency’s concerns.
Ratigan insists he can compete on price while following US laws and running a workplace ethically.
“The reason that I can do this is because the technology allows me to do it in a way that I can compete with even the dirtiest user of slave labor,” he said.
The key, Ratigan said, is a process that’s virtually fully automated: A giant machine fitted with thousands of hand molds dips into a chemical mixture at a precise heat, then at just the right moment pulls off the resulting gloves.
“You could never have done this 30 years ago because the technology didn’t exist,” he said.
Gesturing towards his production line, Ratigan points to what he calls “one simple widget” — his shorthand for most anything that could be manufactured in the US by a well-paid workforce.
“There are hundreds of these widgets that should be made here and could be made here in a way that provide minimum wages of $50,000 a year, full benefits … no slave labor, no abuse and still create profitable companies,” he said.
USMGC’s minimum wage is $25 per hour, plus health care coverage and benefits — and there are plans to provide free on-site child care, Ratigan said.
“If you treat people as valuable, you always make money,” he said.
Demand-driven flexibility is key, expert says
The pandemic proved that the United States’ overreliance on Asia for medical supplies is “very high risk,” said Prashant Yadav, a health supply chain expert at the Center for Global Development in Washington.
The success of American glove producers depends on how much they can automate and whether they’re flexible enough to ramp production up or down to match demand, he told CNN.
It also depends on how long buyers remember the desperate scramble to secure PPE, Yadav said, “Or is this just a very short-term memory, and soon people will go back to thinking about ‘who’s my lowest cost supplier?'”
In the long term, the US government should help domestic PPE producers by negotiating trade agreements that ensure comparable wages in Asian factories — rather than subsidizing US firms, he said.
“Once the largest set of suppliers who export to the US raise their standards, both on quality and ethics, then everybody in the market is forced to raise their standard,” he said.
Momin and Ratigan agree.
“The US government needs to be courageous and step up and, at the very least, institute the necessary tariffs to punish those who use slaves who produce counterfeit items, including medical gloves, and allow American competitors, like ourselves, to compete on a level playing field,” Ratigan said.
But once his and other plants are up and running, the US should not be quite as vulnerable in sourcing PPE — if and when the next pandemic erupts.
The-CNN-Wire
™ & © 2022 Cable News Network, Inc., a WarnerMedia Company. All rights reserved.
Tim Lister, Florence Davey-Attlee, Darren Bull, Luke Wolagiewicz, Gary Levens, Dougla Burns, Nick Young and David Lynch contributed to this story.