OSU study finds why pulsed sparks improve ignition
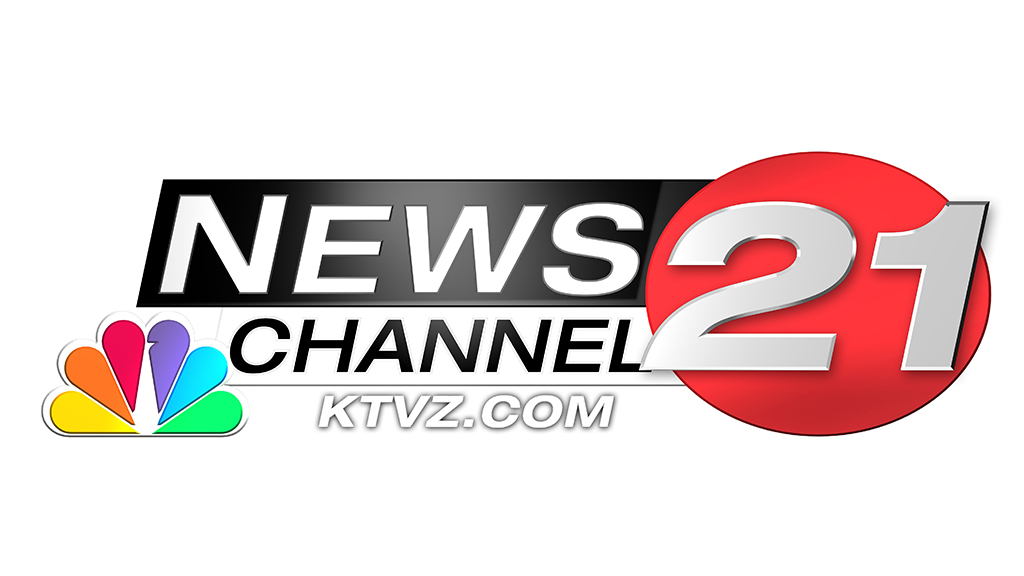
Researchers in the Oregon State University College of Engineering have learned the mechanisms behind a means of improved ignition, helping to open the door to better performance in combustion systems ranging from car engines to jet propulsion.
The findings are important because reliable ignition is a linchpin for the safe and efficient operation of every type of combustion system.
Supported by the Office of Naval Research and the Air Force Office of Scientific Research, the study was built around trying to identify why an improved ignition approach increased the probability of ignition of scramjets, a high-propulsion system that evolved from the ramjet technology of the 1960s. Scramjet is shorthand for supersonic combustion ramjet.
Both ramjets and scramjets use their vehicles’ supersonic airspeed – greater than the speed of sound, 767 mph at sea level – and the shape of the inlet valve to compress air prior to the adding of fuel and ignition in a combustion chamber.
In a ramjet, the air being compressed is slowed to subsonic speeds within the engine, but in a scramjet, it is not. That gives scramjet-powered vehicles the potential to reach 20 times the speed of sound – or Mach 20 – compared to the top speed of about Mach 5 attainable with a ramjet.
Studying under OSU assistant professor of mechanical engineering David Blunck, doctoral student Jonathan Bonebrake traveled to Dayton, Ohio, to work with a research group headed by Tim Ombrello of the U.S. Air Force Research Laboratory.
There, Bonebrake used a high-speed infrared camera to record the effects of nanosecond pulsed high-frequency discharges on ignition kernels, the balls of hot gas that form just after ignition but before the development of a freely propagating flame.
Infrared refers to the part of the electromagnetic spectrum where the wavelengths are longer than visible light but shorter than microwaves. The fuel in the study was a methane and air mixture.
It was already known that the nanosecond pulsed high-frequency discharges – sparks occurring with a frequency in excess of 10 kilohertz, or more than 10,000 times per second – led to improved ignition.
“But why was there enhanced ignition?” Blunck said. “There were some strong theories, but no one knew for sure.”
Bonebrake and Blunck developed an “inverse deconvolution technique” to determine the changing temperature and size of the ignition kernels based on the infrared images and tested the technique successfully against experiments conducted with a McKenna burner, a standard tool in combustion studies.
“With our camera, we could measure the radiation and then back out the temperatures of those balls of hot gas as those flame kernels were growing,” Blunck said. “We could quantify the differences in the temperatures of the kernels.
“As we increased the increased the frequency of the spark discharges, there was more energy and more ignitability,” he said. “If the sparks were too far apart, they couldn’t interact, but when the frequency was higher, energy was deposited more efficiently, resulting in higher temperatures and better ignition.”
And not only did increased frequencies lead to an increase in kernel temperatures, Bonebrake noted, but also an increase in how quickly the kernel temperatures grew. The rate of kernel growth can be crucial to ignition success and combustion completion, as the developing kernel can be affected by whatever fluid motion is taking place within the combustion system.
“Tim’s group had observed what the nanosecond pulsed high-frequency discharges were doing, and we were able to explain the ‘why,'” Blunck said. “Now there’s a stronger case for maturing that technology if they choose to try to do that.”
Findings were published in Proceedings of the Combustion Institute.